Warum habt ihr euch für die Anschaffung einer Fräsmaschine entschieden? Wie habt ihr Eure CADCAM Arbeiten vorher produziert?
Zu Beginn haben wir unsere digital geplanten Fräsarbeiten bei Fräszentren produzieren lassen. Die sind zwar in vielen Fällen relativ günstig, aber wir waren mit den gelieferten Qualitäten nicht zufrieden. Was nützt mir ein Käppchen um 35€, wenn sich das Ergebnis nicht mit unseren Qualitätserwartungen und den unserer Kunden deckt? Und so haben wir uns relativ rasch mit Alternativen auf dem Markt beschäftigt. Seit November 2018 steht nun eine PrograMill PM7 bei uns im Haus.
Der Markt für Fräsmaschinen bietet ein enormes Angebot. Warum habt ihr Euch gerade für die PrograMill PM7 von Ivoclar Digital entschieden? Welche Kriterien waren Euch besonders wichtig?
Zunächst haben wir zum Testen ähnliche Arbeiten an andere Labors vergeben, wo wir gewusst hatten mit welchen Fräsmaschinen produziert wird. Dann haben wir uns die Ergebnisse genau angeschaut. Ein weiteres wichtiges Kriterium war die Servicequalität. So eine Maschine muss fast rund um die Uhr einsatzbereit sein. Daher wollten wir einen Hersteller, der einen eigenen Support in Österreich anbietet. Den Kauf haben wir über ein Depot – in dem Fall Henry Schein – abgewickelt, bei technischen Fragen gibt es eine – bis jetzt – gut erreichbare Hotline mit kurzen Responsezeiten direkt vom Hersteller. Bei kleineren Problemen kommunizieren wir über Teamviewer. Falls größere Probleme auftauchen sollten, kommt jemand vorbei. Die Produktion in Bürs ist ja nur knapp 100km entfernt (lacht). Ein weiterer Grund für die Entscheidung ist unser Kommissionslager. Wir haben ständig alle Materialien und alle Werkzeuge auf Kommission hier im Haus und können rund um die Uhr arbeiten. Wenn wir durch irgendeinen Lieferverzug drei Tage kein Lithiumdisilikat fräsen könnten oder vier Tage kein Zirkonoxid wäre das ein riesiges Problem. Mit dem Kommissionslager sind wir auf der sicheren Seite.
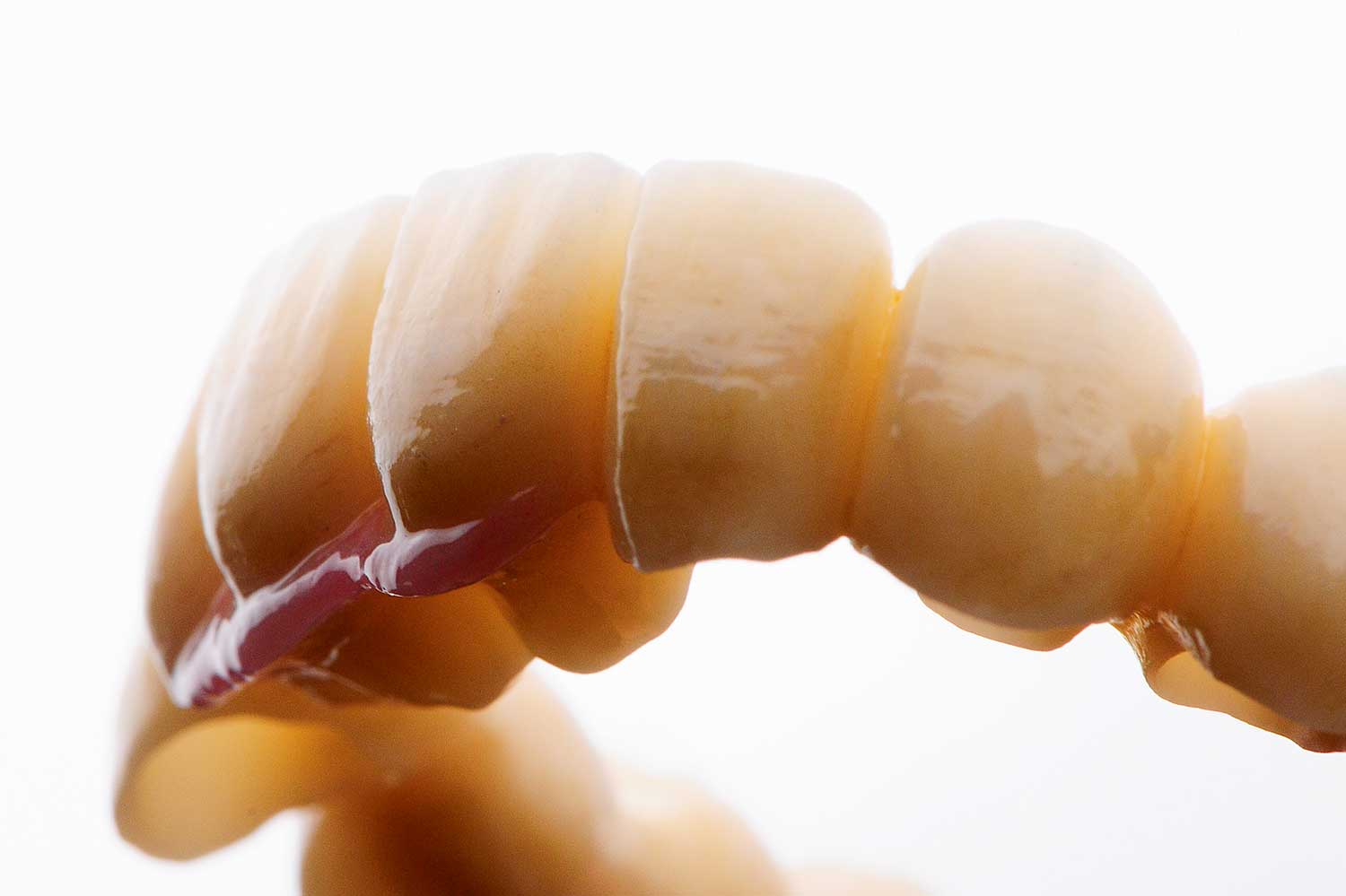
Auf welchen digitalen Workflow setzt Euer Labor? Welche Rolle spielen Intraoralscanner und 3D Drucker?
Noch sind wir nicht ganz von der Präzision der aktuellen Intraoralscanner überzeugt. Bei uns startet der Workflow mit dem Scan der Modelle. Das ist ausgereift und sehr exakt. Der Laborscanner und die Planungssoftware stammen von 3Shape, einem Partner von Ivoclar Digital. Die CAM Software zum Fräsen inklusive der Algorithmen zum Nesten stammt von Ivoclar Digital selbst. Wir brauchen uns somit keine Gedanken über irgendwelche Frässtrategien zu machen, da das alles für die jeweiligen Restaurationen von Ivoclar direkt im System hinterlegt ist und ständig erweitert wird. Updates werden zeitnah vom Hersteller direkt eingespielt, sodass wir immer up-to-date sind. Aus der CAM Software werden dann die Projekte an die PM7 geschickt und es geht los.
Das heißt, Ihr nehmt die Vorschläge 1:1 aus der Software an?
Nein, normalerweise nicht. Man kriegt natürlich einen brauchbaren Vorschlag direkt aus der Planungssoftware. Aber ein versierter Zahntechniker, der weiß, wo die Kontaktpunkte sind oder der noch analog eine Zahnform modulieren kann, sei es in Keramik oder Wachs, tut sich digital viel leichter. Wenn man keine Erfahrung hat, nimmt man automatisch alle Vorschläge aus der Maschine an. Alles, was aus der Maschine kommt, ist für unser Labor aber nur Rohmaterial. Selbst den Grünling der geschliffen aus der Maschine kommt, den bearbeite ich nach. Nach dem Sintern ebenfalls, da gebe ich noch eine Oberflächenstruktur dazu. Ein Vorteil durch die monolithische Krone aus Zirkon ist ja, dass man kaum oder gar nicht mehr schichten muss. Die Zeit, die ich mir beim Schichten spare, stecke ich dann ins Malen hinein. Da kann man extrem viel rausholen. Das ist höchst individuell. Bei 10 Zahntechnikern käme man zu 10 verschiedenen Ergebnissen. Von unbrauchbar bis Weltklasse. Daher ist auch die Angst unbegründet, dass alle Fräsarbeiten am Ende ident aussehen. Das technische wie Passungen etc. das ist natürlich überall ident, aber die fertige Arbeit durch die vielen Eingriffsmöglichkeiten niemals. Unsere Kunden schätzen daher unseren Qualitätsanspruch, unser Know-How und die Liebe zum Detail.
Aber um auf die Frage zurückzukommen: Ja, man kann es sich durch die ausgefeilte Planungs- und Frästechnik leicht machen. Aber für wirklich ästhetisch anspruchsvolle Arbeiten braucht es das Wissen und die Erfahrung eines Zahntechnikers. Wenn man im digitalen Workflow mit der Erfahrung aus der klassischen Zahntechnik nur ein wenig eingreift, erreicht man Ergebnisse von 100 zu 1. Wir schauen uns auch jede Arbeit vorher genau an und überlegen mit welcher Technik – manuell oder digital – wir das beste Ergebnis erzielen. Ein Onlay z.B. das moduliere ich mit der Hand und presse es.
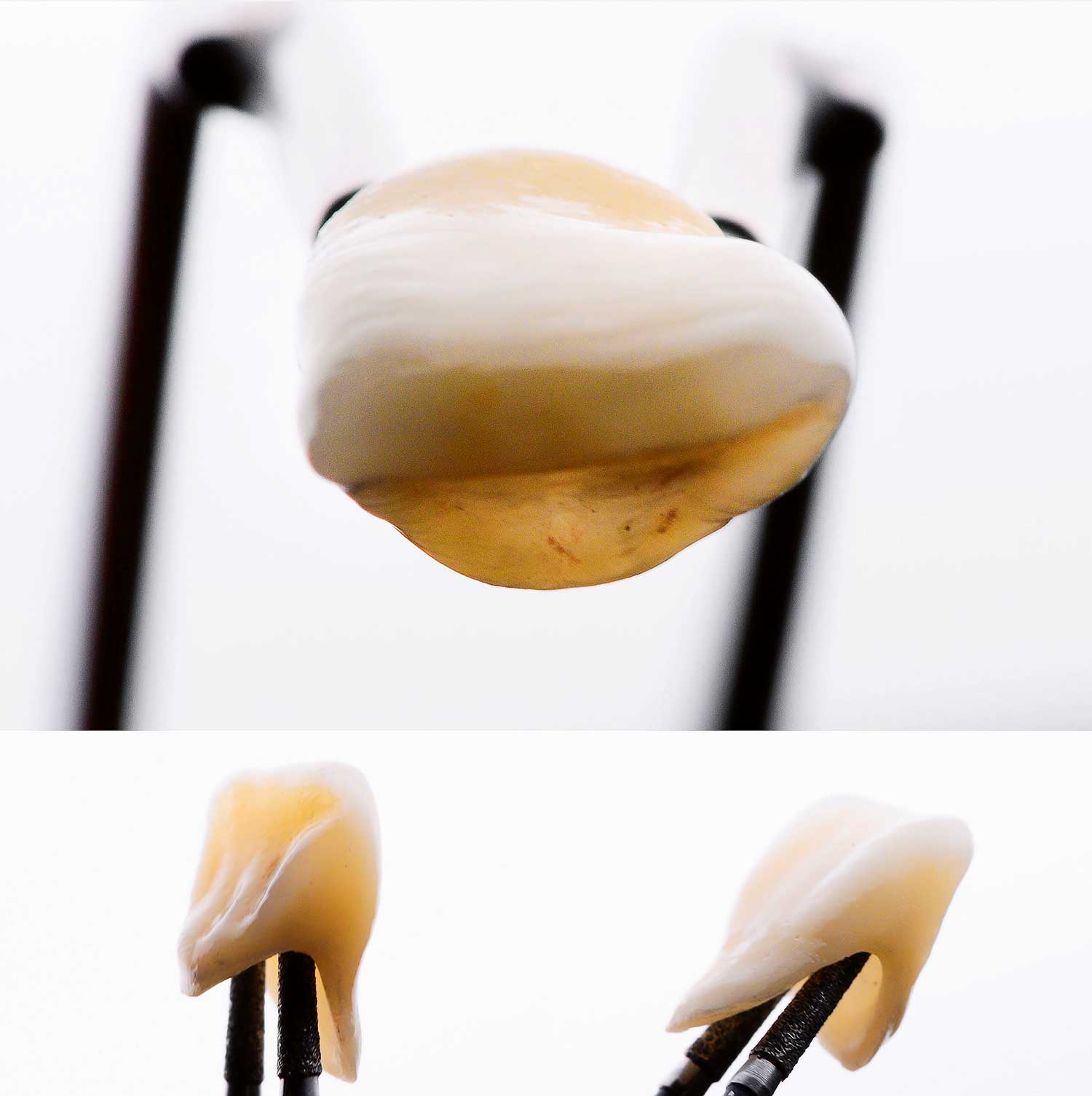
Wie ich sehe, habt ihr nicht nur die Fräsmaschine selbst gekauft, sondern etliches an Zubehör, wie den Unterschrank (Base) oder die darin verbaute Absaugung (Suction Unit)?
Die PM7 ist aus meiner Sicht ein System, nicht einfach nur eine Fräsmaschine. Daher haben wir das Komplettsystem gekauft, da ist jedes Teil aufeinander abgestimmt. Der Unterschrank ist ja nicht nur einfach nur ein Stahlschrank, sondern es ist auch auf die Absaugung, Materialaufbewahrung und die Filtersysteme abgestimmt. Es gibt so keinerlei Staub, das System ist immer sauber – auch durch den abgerundeten Arbeitsraum und den leichten Unterdruck beim Fräsen. Es geht ja auch um unsere Gesundheit, wer will schon den ganzen Tag Zirkonstaub einatmen? Das wäre sparen an der falschen Stelle.
Durch die Suction Unit kann man ganz einfach von trocken auf nass und von nass auf trocken wechseln. Um im gesamten System zu bleiben verwenden wir ausschließlich Werkzeuge, Blöcke und Ronden von Ivoclar Digital. Natürlich kann man auch mit günstigeren Alternativen herumexperimentieren, aber das ist nicht unser Zugang – auch wenn es möglich wäre.
Hat die Anschaffung Reaktionen bei Euren Kunden ausgelöst?
Ja, sehr positive. Wir haben sogar zwei Neukunden dadurch gewonnen. „Ah, Ihr habt die neueste Fräsmaschine“. Denen ist wichtig, dass der komplette Workflow bei uns durchgeführt wird – alles aus einer Hand sozusagen. Und natürlich wissen sie auch, dass die Maschine im Haus – im Fall der Fälle – auch kürzere Durchlaufzeiten ermöglicht. Bei unseren bestehenden Kunden hat die Anschaffung ebenfalls für positive Resonanz gesorgt.
Und bei den Mitarbeitern?
Wir setzen unsere Mitarbeiter möglichst nach Vorlieben und Spezialkönnen ein. Wenn einer sich mit den digitalen Prozessen und Geräten leicht tut und die digitale Planung liebt, dann bitte, setzen wir ihn auch dort ein. Umgekehrt gibt es Mitarbeiter, die sehr gerne analog arbeiten und es beispielsweise lieben mit Presskeramik zu arbeiten. Daher ist uns wichtig unser analoges Know-How zu bewahren und weiter auszubauen, parallel zum digitalen. Das ist genau das, warum uns unsere Kunden so schätzen. Weil wir eben beide Welten beherrschen.
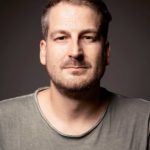
Wieviel Materialien und Werkzeuge könnt ihr nutzen? Womit arbeitet ihr überwiegend?
Wir können in der PM7 zwar acht verschiedene Materialien verwenden und zwanzig Werkzeuge, aber am meisten arbeiten wir mit Zirkonoxid gefolgt von Lithiumdisilikat und natürlich PMMA für Provisorien.
Probleme bisher mit Materialien oder Maschine?
Sehr wenig. Vieles hatte mit unserer Unerfahrenheit zu Beginn zu tun, es gab natürlich mittlerweile auch ein paar Softwareupdates für die PM7, was Indikationen erweitert und Prozessabläufe verbessert hat. Dafür steht ja auch Ivoclar digital. Jetzt läuft alles rund.
Und mit dem Material? Es wird immer wieder über Probleme mit Zirkon berichtet.
Zirkon ist nicht gleich Zirkon. Deshalb setzen wir auf das Material direkt vom Hersteller. Aber noch ein paar Worte zum Zirkon. Wenn man Zirkon richtig bearbeitet und sintert – mit einem exakt kalibrierten Sinterofen – ganz wichtig – dann gibt es keine Probleme mit Chipping. Zirkon ist ein schlechter Wärmeleiter, dahr muss es mit geringen Steigraten gebrannt werden – teilweise mit Steigraten von unter 15 Grad. Genau so wichtig ist eine ausreichend lange Haltezeit und eine auf das Material angepasste Abkühlphase. Wenn man das nicht genau nach Herstellerangaben gut dokumentiert durchführt, dann kann es zu Problemen wie z.B. Mikrorissen oder Abplatzungen kommen.
Hat so eine Maschine auch ein Einsparungspotential? Kann man so eine hohe Anschaffung auch wirtschaftlich argumentieren?
Zunächst einmal bist Du durch so eine Maschine flexibler, die Qualität steigert sich durch die Reproduzierbarkeit. Natürlich könnte man in unserer Größe ca. 1,5 Zahntechniker einsparen, wenn die Maschine gut ausgelastet ist, auch wenn das für uns kein Thema ist. Für uns hat das eher den Vorteil, dass wir alle seit der Anschaffung immer pünktlich heimgehen. Damit leistet die Maschine auch einen Beitrag zur Mitarbeiterzufriedenheit und sie bringt Ruhe in die Firma.
Wie wichtig ist es für Zahnlabore sich mit CADCAM zu beschäftigen?
Um es einmal festzuhalten, CADCAM ist nicht die Zukunft, sondern die Gegenwart. Wer sich bis jetzt nicht mit der Technik beschäftigt hat, hat ein Problem.
Zahnmanufaktur Ges.b.R.
Die Zahnmanufaktur Ges.b.R. gibt es seit 2015 und wurde von den beiden ZTM Manuel Gassner und Gerald Föger gegründet. Neben den Gründern beschäftigt die Firma sieben weitere Mitarbeiter.
ZTM Manuel Gassner
ZTM Gerald Föger
Tel. +43 664 91 34 444
gassner@die-zahnmanufaktur.at
Gewerbestraße 2
6430 Ötztal Bahnhof